1. 引 言 某水下航行体在发射出筒后,在水中竖直向上运动,出水后在空中自由飞行,到达最高点后下落,然后在水中下沉,到达最低点后再上浮,最后漂浮在水面上。航行体回落入水后,可能发生与发射装置碰撞的危险。出于安全性的考虑,航行体在水下发射后必须进行减速控制,并使其速度保持在一定范围,从而间接地保证回落入水的最大深度小于发射装置最高点的深度。舵板是实现此功能的重要部件,当水下航行体以一定速度进入水中时,舵板迅速张开至一定角度,增加航行体在水中的阻力,对航行体进行减速控制。在减速过程中,舵板在水流的冲击下迅速张开,在到位的瞬间突然制动,舵板承受了巨大的水动力冲击载荷,舵板本体和耳座处均产生很大的冲击应力及应变( 见图 1) 。卸载后,弹性变形恢复,塑性变形及部分应力残余在结构中。出于经济性和安全性的考虑,需要评估舵板及其系统主要零部件在多次过载后的剩余冲击寿命。在应变分析和低周疲劳的基础上,现采用一种新的疲劳寿命估算方法———局部应力应变法,此法思路是: 零构件的疲劳破坏都是从应变集中部位的最大应变处起始,并且在裂纹萌生以前都要产生一定的塑性变形,局部塑性变形是疲劳裂纹萌生和扩展的先决条件。因此,决定零构件疲劳强度和寿命的是应变集中处的最大局部应力和应变。其基本假设是: 若同种材料制成构件的危险部位最大应力应变历程与一个光滑试件的应力应变历程相同,则它们的疲劳寿命就相同。
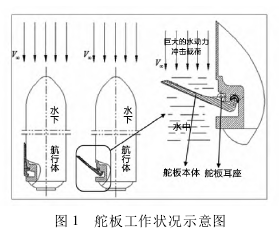
因此,本文针对有应力集中部件的疲劳寿命,通过对其光滑试件进行冲击疲劳试验,确定冲击次数,对结构的使用寿命进行预测。 2 试件制备与试验方法
2. 1 试件制备 2. 1. 1 取样位置确定 本文选取受到 3 次入水冲击后的舵板作为试验对象,其材料为 18Cr2Ni4WA,试件取样位置如图 2所示。
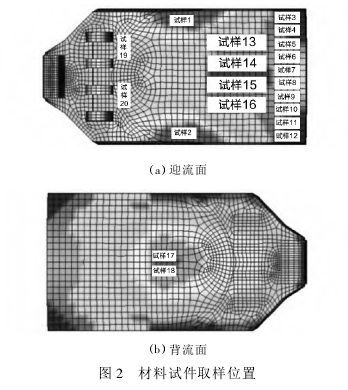
2. 1. 2 试件制备 按照 GB /T229-2007《金属材料 夏比摆锤冲击试验方法》对图 2 所示的试件号 6、7、8、9,进行标准夏比 V 型缺口试验。对试件号 1、2、3、4、5、10、11、12、17、18 进行标准无缺口加工,试件加工尺寸参看图 3 和图 4。缺口加工方法采用定型砂轮磨制或铣床加工,缺口部位应避免划伤。应变片贴于试件中部,所有试件制备情况见图 5。
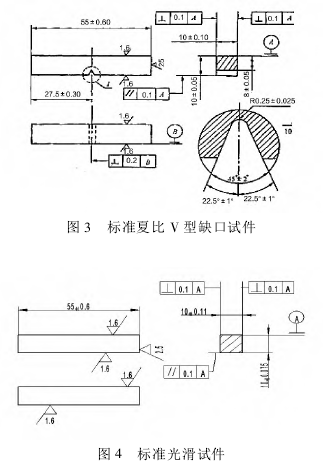
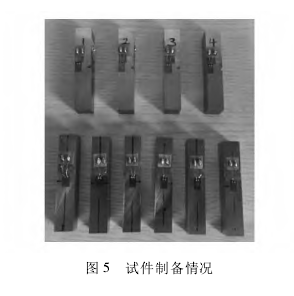
2. 2 试验方法 2. 2. 1 试验设备 及原理采用的试验设备为美国 MTS 公司 ZBC2000 系列( 最大冲击能 300J) 摆锤冲击试验机( 见图 6) ,其控制系统采用 PLC 控制方法。该设备由旋转编码器来获取摆锤的实时位置,具有抗干扰能力极强,可靠、稳定、数据准确等特点。采用单向应变计,型号为 BX120-10AA,测试系统的量程为 20000με,超过该范围的数值不作为评价依据,仅供参考。应变测试采用 DASP -V10 动态应变采集系统。试验方法为: 将试件放置在砧座上,通过设定摆锤的冲击能对试件进行不同能量的冲击试验,观察试件的断裂及变形情况( 见图 7) 。本次试验对于含缺口试件进行一次冲击,对于光滑试件进行多次冲击,观察冲击后的试件宏观形变与微观应变特征。
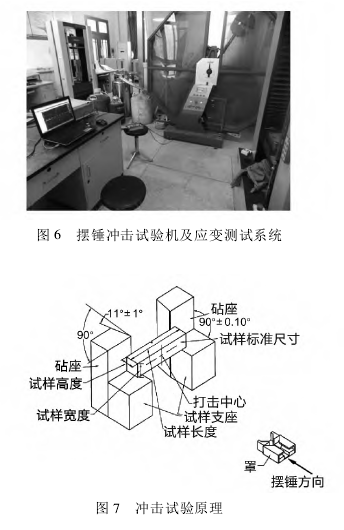
2. 2. 2 冲击能量确定 摆锤大能量冲击理论是根据应力应变法的基本假设,即若同种材料制成的构件的危险部位的最大应力-应变历程与一个光滑试件的应力应变历程相同,则它们的疲劳寿命就相同。因此,在按照国标进行摆锤冲击试验时,冲击能量的确定是依据实际工况中舵板上危险部位的应变水平。根据前期仿真结果,选取模型中舵板厚度变化处、等效应力相对较大的某个单元,测得其应力峰值可达到 0. 85GPa 左右。根据该单元的应力、应变分量,计算其应变能为:
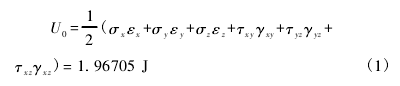
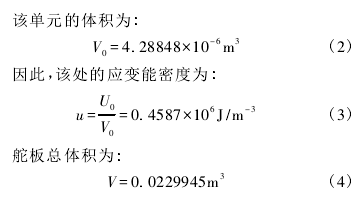
按照该应变能密度计算,舵板的总应变能最多应为 10. 55kJ,大于直接测得的真实总内能( 应变能) ,峰值为 7. 082kJ,即:

这说明,使用应变能密度 458. 7 kJ/m3作为从大尺度舵板到小尺度摆锤冲击试验件进行尺度和冲击能量缩放依据,具有一定的可比性。 根据国标,光滑无缺口的冲击试件的体积为:

使得光滑无缺口的冲击试件达到 0. 85GPa 的等效应力水平时需要吸收的应变能为:

通过对舵板应变较大危险点的应变进行实测,直接得到了 0°、90°和 45°方向的应变。当测量时间t = 19. 58s 时,3 方向的最大应变分别为:
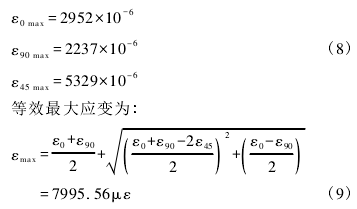
首先对光滑试件预试验冲击,得到当用 6J 能量对光滑试件进行冲击时,应变片粘贴处的实测应变为 8753. 966με,大于公式中危险点的 7995. 56με,表明 6J 冲击能量刚好接近实测工况下的舵板受载情况。为研究不同能量冲击对舵板的影响,冲击试验时分别选取了 6J、8J、10J、15J 和 20J 等 5 种能量进行多次冲击。
|