1 .引 言 电动汽车由于污染小、噪声低,具有节能、环保的优势,可有效缓解能源资源紧张、大气污染严重等问题,受到了许多国家的高度重视。所谓纯电动汽车,是指以电能为动力的汽车。电动汽车的组成包括电力驱动及控制系统、驱动力传动等机械系统、完成既定任务的工作装置等。电动汽车无内燃机汽车工作时产生的废气,不产生排气污染,对环境保护和空气的洁净是十分有益的,有“零污染”的美称。日前所推出的新型纯电动汽车,在急加速然后松踏板的瞬间,出现了明显的抖动现象,给乘员的主观感受极度不舒服。本文针对这一现象,以新型纯电动汽车为平台展开研究。 2 .新型纯电动汽车振动源分析 新型纯电动汽车的结构如图 1 所示。从外形上看,电动汽车与传统汽车并没有什么区别,但纯电动汽车的动力总成是由动力源及驱动系统、动力电池、驱动电机和控制器 3 个部分组成的,其电机相当于传统汽车的发动机,蓄电池相当于原来的油箱,通过电池向电机提供电能,驱动电动机运转,从而推动汽车前进。
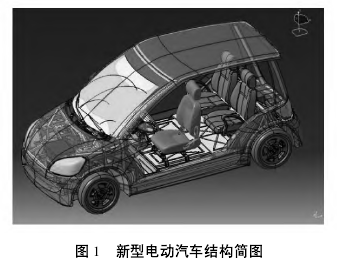
本文研究的新型纯电动微型车为前置前驱型,其动力驱动系统布置在前舱内,主要包括集中电机、减速箱及差速器并通过悬置连接到副车架,副车架再通过悬置连接到主车架。其主要振动源是包括集中电机、减速器和差速器在内的驱动系统,由路面不平度引起的轮胎振动也是新型纯电动汽车振动的一个主要来源。新型纯电动汽车振动的传递路径如图 2 所示。
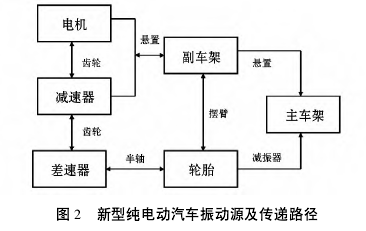
3 .新型纯电动汽车声振测试 由于纯电动汽车的控制系统是通过接收驾驶员的踏板信号对各部件进行相应控制的,所以在松踏板的瞬间,由于突然失去动力的来源,会出现整车抖动现象,尤其是在急加速松踏板工况。针对这一现象,本文进行了急加速松踏板工况下的整车声振测试,以找出引起抖动的源头及传递路径。本次试验在同济大学半消声室进行,试验采用的数采设备为 Head 公司的 SQlabⅢ( 34 通道) ,加速度传感器为美国 pcb 公司生产的 icp 压电式加速度传感器,麦克风为丹麦 B&K 公司生产。 3.1 试验工况 为客观测量并分析纯电动汽车急加速松踏板工况的抖动现象,在转鼓试验台上进行模拟试验,将纯 电 动 汽 车 分 别 急 加 速 到 10km/h、15km/h、20km / h、25km / h、30km / h、35km / h、40km / h 突然松开踏板( 记录时刻) 直到停止。 3.2 测点布置 为准确分析新型纯电动汽车的抖动现象并明确产生抖动的原因,在进行试验时,需进行合理的测点布置。 ( 1) 振动测点: 驾驶员座椅地板垂向加速度 1;车前主车架中部三向加速度 1; 车前副车架中部三向加速度 2; 电机处三向加速度 3; 减速箱( 与电机相连处) 轴承连接处三向加速度 4; 减速箱( 中间齿轮轴处) 轴承连接处三向加速度 5; 减速箱( 差速器处)轴承连接处三向加速度 6; 减振器上三向加速度 7;轮胎处三向加速度 8。 ( 2) 转矩测量: 测量电机转速,电机 - 差速器的输出转矩特性及差速器 - 轮胎的输出转矩特性。 4 .试验结果与分析 人们能够感受到的抖动是来自于主车架振动的突变,因此本文着重分析了急加速松踏板时主车架的振动特点及来源。考虑到试验信号的非平稳性,主要通过小波分析对测试信号进行处理,同时采用相干/偏相干分析、传递函数等方法对数据进行分析处理。 4. 1 抖动现象分析 ( 1) 不同车速下主车架的振动云图图 3 是不同车速工况下主车架的振动云图,可以看出: 在每个车速下,松踏板的瞬间均发生了振动的突变( 即抖动现象) ; 主车架振动突变频率均集中在 10 - 20Hz 的低频段; 抖动的剧烈程度随着车速的增加而减小,即车速越小,抖动现象越明显。
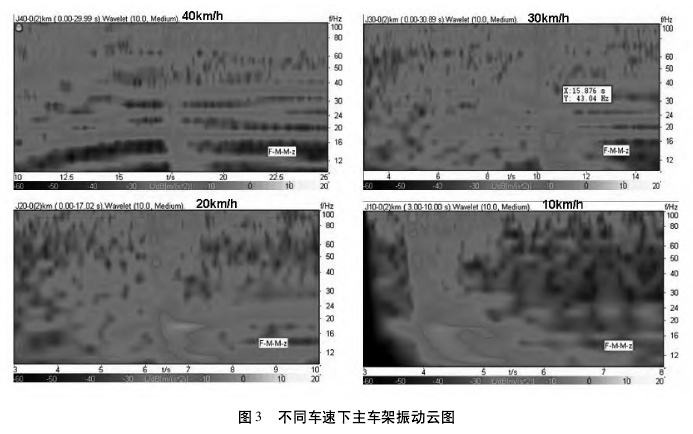
( 2) 振动传递路径云图分析 图 4 是利用各部件的振动云图来表示振动能量在各部件之间的传递,从图中可以看出: 在急加速松踏板工况,出现振动突变的部件为轮胎、电机和减速器、副车架、主车架; 从发生抖动的剧烈程度出发,大小排序为: 轮胎 > 电机和减振器 > 主车架 >副车架; 振动突变的频率均集中在 10 - 20Hz 的低频段。
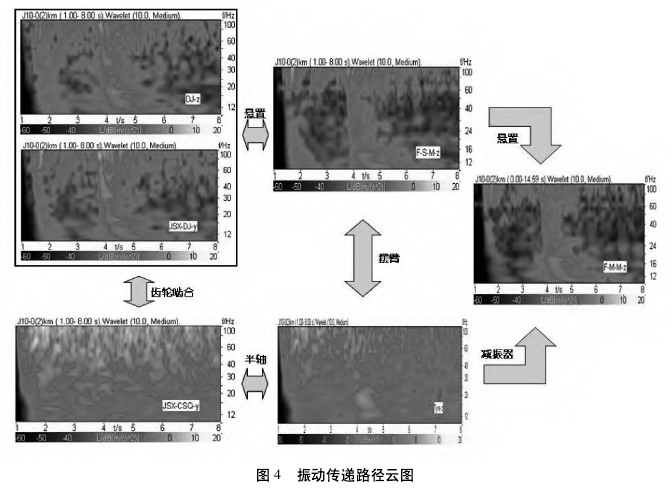
通过对纯电动车急加速然后松踏板工况所采集的主车架振动云图和各部件振动传递的云图分析表明: 纯电动车在急加速松踏板的瞬间存在抖动现象,出现振动突变的部件为轮胎、电机和减速器、副车架、主车架; 车速越低,松踏板时抖动现象越明显; 抖动频率集中在 10 - 20Hz 的低频段。下面将具体分析主车架在急加速松踏板时振动突变的原因。 4. 2 抖动原因分析 通过对新型纯电动汽车振动传递路径的分析可知,主车架振动直接激励源有两个: 一是电机、减速器等动力系统的振动传递到副车架然后再经悬置传递到主车架,另一个是轮胎振动经悬架、减振器传递到主车架。 ( 1) 相关/偏相关分析 为明确主车架在抖动频段振动能量的主要来源,本文对主车架与其激励源副车架和轮胎的振动信号进行了相干/偏相干分析,如表 1 所示。
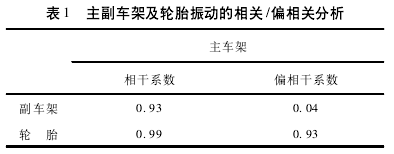
不考虑副车架和轮胎之间振动的相互影响,对主车架与副车架和轮胎振动信号进行相干分析得出: 副车架与主车架之间的振动相干系数为 0. 93,轮胎与主车架之间的相干系数为 0. 99。由于主车架振动的两个直接激励源并不是独立的,副车架和轮胎支架通过摆臂连接,因此考虑副车架和轮胎之间振动的相互影响。对主车架与副车架和轮胎的振动信号进行偏相干分析得出: 副车架与主车架之间的振动偏相干系数为 0. 04,轮胎与主车架之间的偏相干系数为 0. 93。这说明,主车架的抖动能量主要来源于轮胎。同时,轮胎振动通过摆臂对副车架的振动能量的贡献也较大。 ( 2) 主副车架连接悬置性能分析 纯电动汽车的主车架和副车架之间是通过悬置相连接的,悬置的隔振性能的好坏直接决定了副车架的振动向主车架的传递。因此,本文对主副车架之间的连接悬置的传递特性进行了分析,如图 5 所示。图 5 是纯电动汽车主副车架之间连接悬置的传递特性频谱图,可以看出: 该悬置在 10 - 20Hz 的抖动频段内的隔振性能较差,副车架的振动经悬置传递到主车架,起到了放大的作用。因此,该电动车主副车架之间的连接悬置在引起抖动现象的频段内不能起到隔振的效果。( 3) 电机转矩特性图 6 是新型纯电动汽车集中电机的转矩特性曲线,是根据试验测得的不同电机转速下的输出转矩拟合得到的。
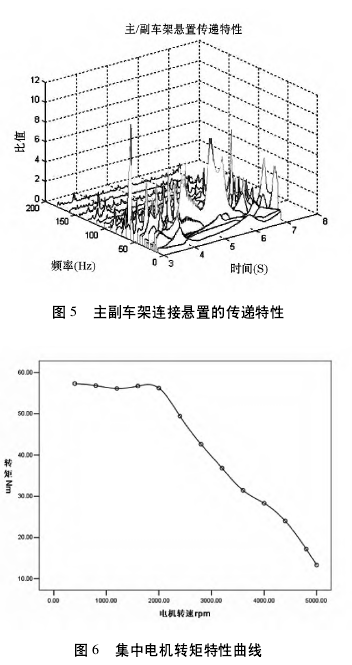
通过振动能量传递的云图可以看出,电机、减速器和轮胎上的抖动频段的能量较大,究其原因,是在松踏板的瞬间,相当于在电机上外加了一个与输出转矩方向相反的力矩,这时轮胎上就会产生一个方向相反的力矩。因此,电机、减速器和轮胎在急加速然后松踏板工况下的抖动较为严重。 新型纯电动汽车车速与集中电机转速之间的换算公式为:

其中: v 为车速,km/h; i 为传动比,i = 11. 8; r 为车轮半径,r = 0. 269m; n 为电机转速,r/min。
通过图 6 和公式 ( 1) 计算可以得出: 车速 <17km / h 时,电机输出转矩基本保持不变; 车速 >17km / h 时,电机输出转矩随车速的增加而减小。因此,新型纯电动车在低于 17km/h 工况抖动现象较明显,高于 17km/h 随着车速的增加抖动现象越不明显。 5. 结 论 本文通过对新型纯电动汽车急加速松踏板工况的声振测试及测试数据的处理分析,可知: ( 1) 在不同车速下均发生不同程度的抖动现象; 车速越低,抖动现象越明显; 抖动频率主要集中在 10 - 20Hz 范围,不随车速变化。 ( 2) 主副车架、电机、减速器、差速器、轮胎都出现了不同程度的振动突变,发生抖动的剧烈程度排序为: 轮胎 > 电机和减振器 > 主车架 > 副车架。 ( 3) 主车架的振动直接影响人们的主观感受,通过对主车架及其振动的两个源头进行相干 /偏相干分析发现,轮胎是主车架抖动的主要来源。 ( 4) 通过对主副车架之间连接悬置的性能分析,发现该悬置在发生抖动现象的频段内隔振效果较差。 ( 5) 通过对纯电动车集中电机转矩的输出特性的分析,由于低速时输出转矩较大,使得低速时抖动现象较明显。因此,要消除或改进新型纯电动车的抖动现象,可以采取以下两种方案: ( 1) 优化主副车架之间的连接悬置,使其在抖动频段内的隔振性能提高;( 2) 优化悬架参数,使轮胎的振动能量尽可能少地通过减振器传递到主车架。 |